UAA researcher senses a solution to pipeline corrosion
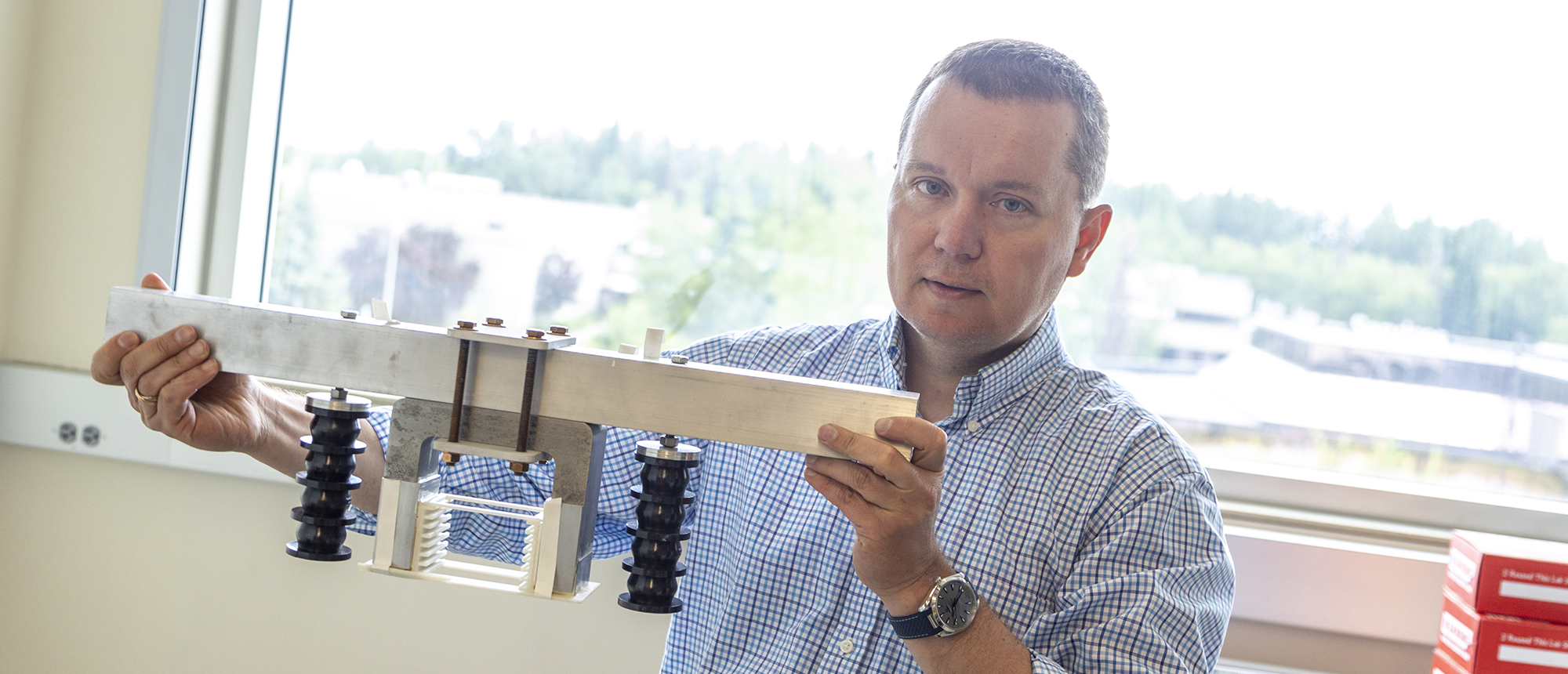
By Joe Selmont
On the North Slope there are thousands of small pipes that ultimately come together to feed into the big one — the Trans-Alaska Pipeline. Each of those pipes are a potential hazard, especially as they experience the effects of air, water and chemistry over long periods of time. Even in the cold of the Arctic, pipes will eventually succumb to corrosion — the natural chemical process that transforms refined metals into oxides. Rust, for example, occurs when iron and oxygen form a chemical bond. If technicians responsible for monitoring those pipes don’t catch corrosion and other forms of degradation before it’s too late, then a pipe could burst, resulting in a problem with serious environmental, financial and public relations consequences.
That’s where Oleg Shiryayev, Ph.D., assistant professor of mechanical engineering in UAA’s College of Engineering, comes in.

“The problem with flow lines, or the small pipes that connect from the wells to the first processing facilities, is that they do not regularly get the same protection as the big boy, the Trans-Alaska Pipeline,” said Shiryayev. “Simply put, there are too many of them. And for that same reason, it is very difficult to adequately monitor all of them.”
To keep an eye on the integrity of flow lines, the current process requires a team of technicians to physically walk around the pipes and inspect them for damage using ultrasound and additional measuring tools. While this method is reasonably effective, Shiryayev points out it is highly inefficient. Plus, it is difficult to access some pipes once they have been installed.
To make matters worse, flow lines and other small pipes are rarely equipped with the launching and retrieval mechanisms that are required to use one of the industry’s most efficient monitoring tools — pipeline inspection gauges, or PIGs. For the larger pipes, and particularly for the 800-mile long Trans-Alaska Pipeline, PIGs enter at one location, get caught up in the flow and then exit dozens or hundreds of miles downstream. During their wild rides, the PIGs use a variety of sensors to capture important data about the integrity of the pipeline.
“But since we cannot monitor flow lines from within using PIGs, we have to monitor them from the outside,” said Shiryayev. “And my project demonstrates the feasibility of using fiber optics and magnetism to accomplish precisely that.”
The details of Shiryayev’s project get a little technical — so buckle up.
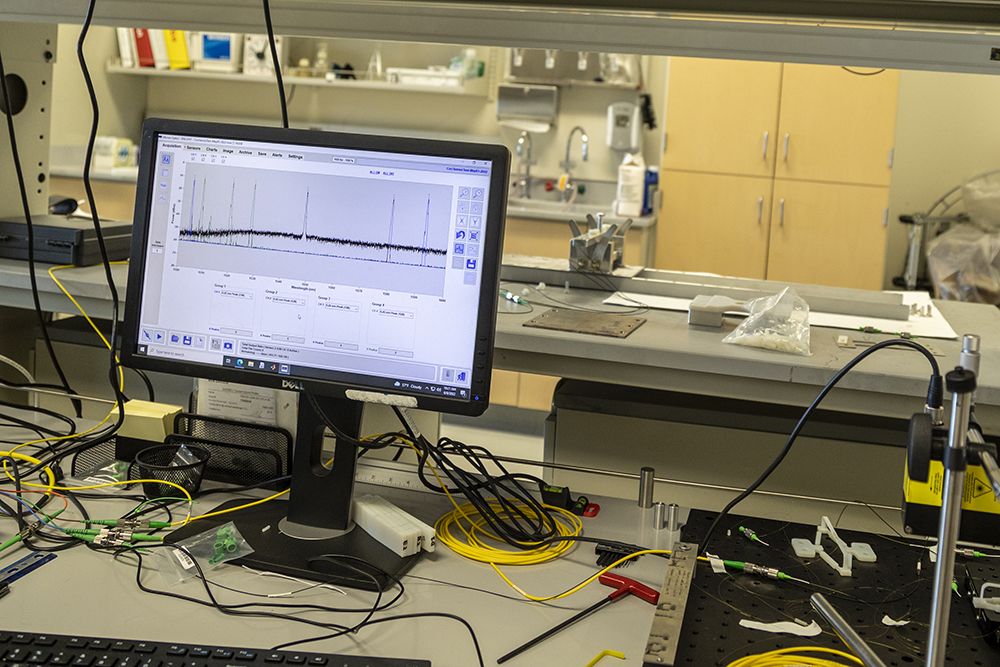
Shiryayev’s core concept is to use a combination of fiber optic strain sensors and a magnetostrictive material, such as an alloy called terfenol-d, to monitor the magnetic flux that leaks out of a pipe as its walls becomes thinner due to corrosion or other forms of damage. Magnetostrictive materials are any substance that can be mechanically deformed by the presence of an external magnetic field. Magnetic flux is a measurement of the total magnetic field passing through a given area.