Student engineers test asteroid anchor at NASA HQ
by joey |
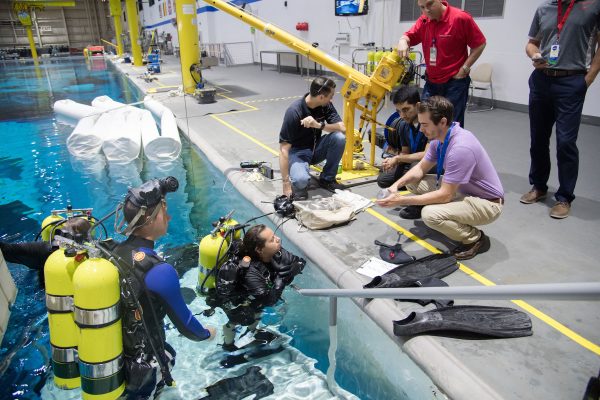
Mechanical engineering students Udayan Dutta and Steven Ahern instruct NASA's dive team on how to use their asteroid anchoring system at the Micro-g NExT event in June. (Photo by Allison Bills / NASA JSC Education)
University of Alaska Anchorage students recently traveled to Johnson Space Center in Houston, where NASA tasked them with developing the next stage of space exploration.
The Micro-g Neutral Buoyancy Experiment Design Team Challenge - known within acronym-happy NASA as Micro-g NExT - annually invites engineering students to tackle a current space design issue.
This year, NASA challenged undergraduates to design an anchoring system that could tether a spacecraft to an asteroid.
For guidance, teams could look to the high-profile faults of the Rosetta probe in 2014. After a decade of transit, the European Space Agency's craft reached its destination comet, but its harpoon-style anchoring system failed to deploy. Instead, its lander bounced across the comet's surface as the European team watched powerlessly from mission control. It was the first successful landing on an asteroid, but it wasn't clean or pretty.

NASA staff greet the teams at the 2017 Micro-g NExT event at Johnson Space Center. Udayan Dutta and Steven Ahern (center column, second row) represented UAA. (Photo by James Blair/ NASA JSC Education)
The engineering students who competed at Micro-g NExT hoped for a different outcome. After submitting an initial design proposal in early October, 29 teams - including UAA's Steven Ahern and Udayan Dutta - flew to Houston to test their prototypes with trained NASA staff.
Over the course of the school year, Ahern and Dutta refined their complex initial model, dropping features like a compressed air system and two-part epoxy binding system.
"It got pretty complex," Ahern said with a laugh. "The more we worked through these designs we realized A) we don't have enough time to complete everything and B) we don't want our prototype to fail when it gets there."

The team's aluminum augur, displayed in the engineering department's student workshop alongside an earlier prototype. (Photo by Ted Kincaid / UAA)
So the UAA team focused on simplicity. "Less mechanisms, we thought, would equal better success," Ahern said.
"We just engineered all the way down to bare bones, as well as we could," Dutta added. "In space, you don't really have a lot of redundancies if you fail, so we wanted to make it as simple as possible."
Anchors matter in microgravity, especially on a swiftly spinning asteroid where centripetal force can rip a lander off the surface. NASA required teams design an anchor that could resist 15 pounds of upward pull. Likewise, completed prototypes had to meet specified height and weight limits, as every bit of excess makes liftoff from Earth more difficult.
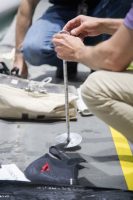
Ahern demonstrates UAA's anchor prototype on the deck of the Neutral Buoyancy Lab in Houston. (Photo by Allison Bills
With help from fellow mechanical engineering graduate Nick Hazelton, Ahern and Dutta designed six iterations of their anchor, fabricating the last three in UAA's machine shop. Both the Alaska Space Grant, based at UAF, and the UAA College of Engineering supported the project.
The team's finished product is a thin, lightweight aluminum augur, so simple it only requires two fingers to turn. But its size belies its sturdiness. "You could stand on this and pull on it and nothing's going to happen," Ahern said.
To test their device, the duo assembled an improvised lab in the engineering department's student workshop. NASA holds the Micro-g NExT event in the simulated weightlessness of its 6.2-million-gallon Neutral Buoyancy Laboratory (NBL), a massive indoor pool filled with submerged spacecraft replicas. Ahern and Dutta, though, devised a humble alternative and simply filled a 55-gallon trash can with sand and water. Their design, they say, responds to the "worst-case scenario:" a comet with a layer of loose soil and sandy grit. During their test runs, the aluminum augur's helical blade easily burrowed into the test sand, and the device resisted plenty more than the 15 pounds of pull.

NASA hosts Micro-g NExT at the 62-million-gallon Neutral Buoyancy Laboratory at the Johnson Space Center in Houston. (Photo by Allison Bills/ NASA JSC Education)
After nearly a year of extracurricular engineering work, the UAA team flew to Houston to test its prototype alongside teams from engineering powerhouses like Cornell and Purdue. Their June 5-8 visit included tours, talks and internship advice. They were even on hand when Vice President Mike Pence announced the next training class of 12 astronaut candidates, including Anchorage's Robb Kulin.
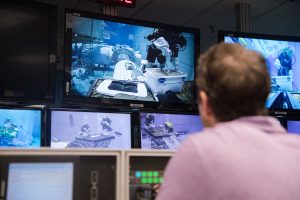
Ahern guides NASA divers from a mission control room at Johnson Space Center. (Photo by Allison Bills / NASA JSC Education)
Test day was a bright and early Tuesday morning. Ahern and Dutta handed their device to NASA divers, then headed to a control room to continue instructing over headsets. They were the first of the 29 teams in the water.
In the NBL tank, divers twisted their augur halfway into a mix of regular sand - a more compact variety than what Ahern and Dutta had prepared for - and attempted to pull it loose, with a scale attached to measure outward force. The anchor didn't budge. In fact, it maxed out the 50-pound scale. There was even enough time left to test the anchor on a rock/sand blend, and it had the same results.
"We don't actually know how much it can hold because it kept maxing out the scale," Dutta said of the second test. "We were thrilled at that point."
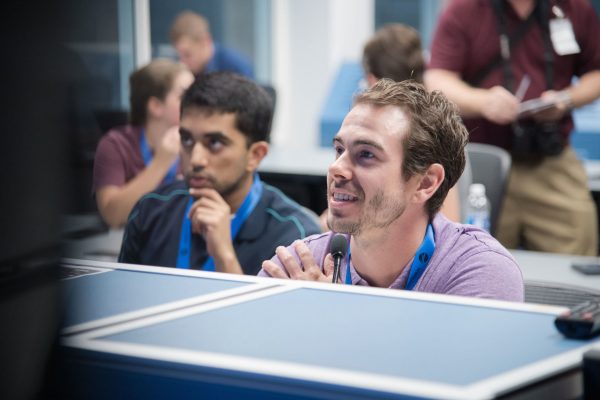
Udayan Dutta and Steven Ahern react in the mission control room after a successful test of their asteroid anchor at Johnson Space Center. (Photo by Allison Bills / NASA JSC Education)
Now that the event is complete, the team would like to thank Denise Thorsen, director of the Alaska Space Grant, and Fred Barlow, College of Engineering dean, for funding their research; Utpal Dutta for serving as the team's faculty advisor; Associate Professor Jeff Hoffman for his ideas; and Corbin Rowe of the college machine shop for manufacturing and guiding their prototypes.
After a year of design, and a successful test, Ahern and Dutta are now focused on what's next after NExT. For Dutta, that's a summer engineering internship at BP in Anchorage. He plans to graduate in December of next year, and credits the faculty and NASA support for "a great experience overall."
Ahern immediately left Houston for a NASA internship at Ames Research Center in Silicon Valley, home of the world's largest wind tunnel, which he credits to connections he made through Alaska Space Grant and UAA faculty. "I'm extremely thankful for all their help."
Ahern hopes to work in aeromechanics after graduating this fall. Ideally, he'd like to stay in NASA's orbit a little bit longer. After a successful run in the Micro-g tank, that's definitely a down-to-earth possibility.
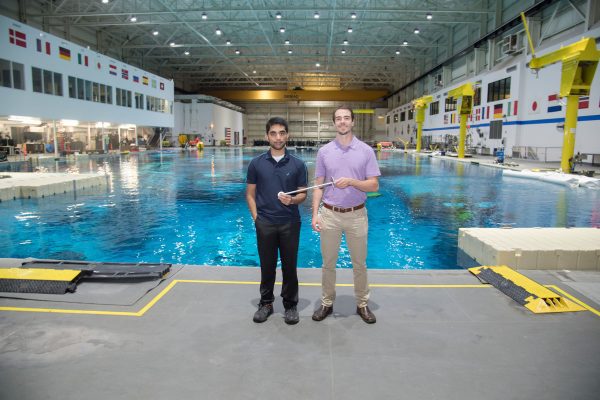
Udayan Dutta and Steven Ahern, displaying their anchor from Anchorage at NASA's Neutral Buoyancy Laboratory. (Photo by Allison Bills / NASA JSC Education)
Written by J. Besl, UAA Office of University Advancement
