Engineering college helps man on a warm-house mission
by Kathleen McCoy |
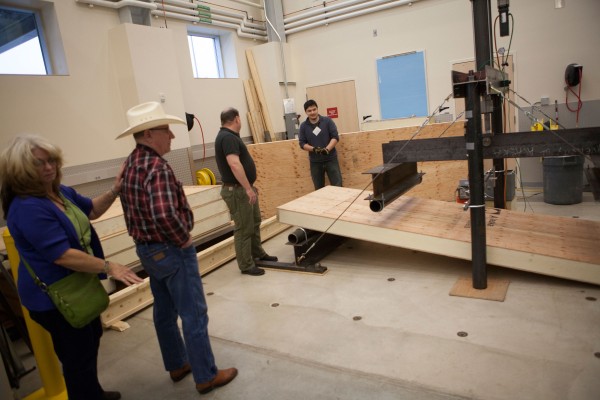
Ron Burkhardsmeier, a manufacturer of foam panels in Wasilla, watches his design undergo testing at the Engineering and Industry Building at UAA. He waited almost two years for UAA to open the lab so he could get testing done in the state. (Photo by Philip Hall / University of Alaska Anchorage)
Ron Burkhardsmeier is a one-man economic engine rarely found in Alaska: he's a manufacturer.
From his Wasilla facility, he and five to nine employees are busy manufacturing warm walls for houses in extreme climates. He started out buying walls for his house kits from Canada. After NAFTA limited him to domestic sources, he found some in the Lower 48. But travel damage and quality issues turned this 76-year-old into a self-taught manufacturer.
"If I'm going to have control over the quality of this product, I have to make it," he said. It helps to know he grew up on a North Dakota ranch, son of a man who had to fix or invent every tool he used. Faced with a similar challenge, Burkhardsmeier sold off his assets so he could buy a foam machine and a press, and learn to build the walls he knew would work for Alaska.
These walls are called foam core panels, SIPs for short (structural insulated panels). Think of a sandwich as tall and wide as your living room wall. The filling is a fat slab of polyurethane foam heat-fused between two plywood slices. His walls end up in custom home designs (bring a floor plan and his team customizes walls to fit), or more simply, buy a house kit and put it together yourself.
With siding added, you can't tell a SIP house from a stick-frame house, except for the cost. Burkhardsmeier's house will be 5-10 percent pricier. The upfront cost is recovered with heating savings, he says
"If you're burning 800 gallons of fuel oil to warm a 1,000-square-foot home, at $5 a gallon, that's $4,000. What if it was just 100 gallons, or $500?"
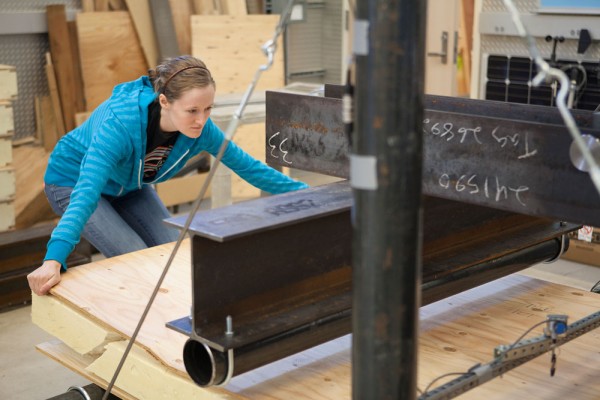
Undergraduate Stephanie Petersen works with an insulated panel during a materials test in the new engineering building. (Photo by Phillip Hall / University of Alaska Anchorage)
Another way to say it: He builds a house you can afford to live in later.
Energy-efficiency, with 5- and 6-star ratings, is his standard. Rural Alaska's 10,000-unit housing shortage is his primary market. But he also has his eye on Anchorage.
He lives in one of his own houses in Wasilla, 1,800-square-feet with three bedrooms. His wife claims the house is so tight she can go a month without dusting. He's personally built 26 of them in Wasilla and about 20 more in rural villages. Altogether, he's sold or customized 350 statewide.
So why did Burkhardsmeier wait almost two years for UAA to open its new engineering building? Because it has a strong floor, and professors and students, who could help him test the strength and capacity of his manufactured walls.
His design is original in that he replaced the typical outer skin with plywood. Plenty of manufacturers create these walls using "oriented strand board," or OSB. You've seen it-wood particleboard formed by compressing adhesive and wood strands or flakes.
"I call it 'overnight saturation board," Burkhardsmeier says ruefully. In wet regions, or in transit aboard shipping barges, the OSB "absorbs water and swells up." High quality plywood solved that problem, but Burkhardsmeier needs testing data to demonstrate strength.
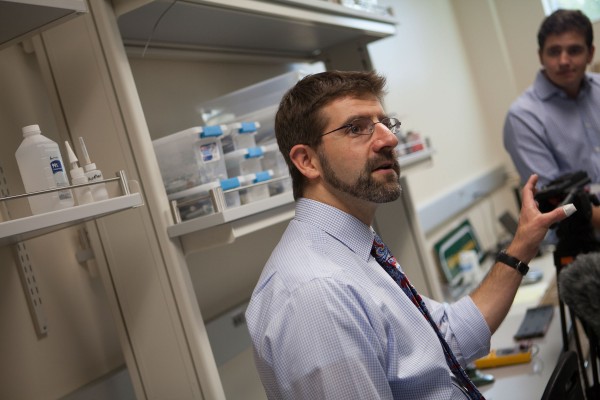
Scott Hamel, professor of structural engineering. (Photo by Phillip Hall / University of Alaska Anchorage)
Scott Hamel, a structural engineering professor who teaches steel design, concrete design, and structural loads, plus a handful of undergrad and grad students, signed on to tackle bending, compression and racking tests on Burkhardsmeier's walls. By having his tests done in Anchorage, he's saving about $20,000 in shipping and Outside testing costs, Burkhardsmeier said.
It's a happy relationship. Hamel and his students get to work on a real-world problem, including designing and building the giant fixtures that perform the tests. Burkhardsmeier gets data to show building inspectors and architects the true quality and reliability of his product.
"I am a made-in-Alaska product," he said. "When I heard they were building that science lab, I waited for it."
But there's more. While Burkhardsmeier retains the intellectual property on his walls, Hamel gets to write about them for engineering journals. And Hamel has a few modification ideas of his own.
SIP panels come in only certain lengths, like eight, nine and 10 feet. Hamel would like to build a tall wall, say 16-18-20 feet, by splicing walls together. He's already imagining how to model the design on a computer, and if that works, build and test it on the strong floor.
Hamel said Burkhardsmeier is not the first manufacturer or engineering entrepreneur to approach the engineering college for some testing; more are lining up.
That's encouraging. Diversifying Alaska's economy will be a huge task. But stories like this give nod to that old saying: How do you eat an elephant... one bite at a time. How do you remake an economy? One idea at a time. It's a start.
A version of this story by Kathleen McCoy appeared in the Alaska Dispatch News on Sunday, Dec. 6, 2015.
